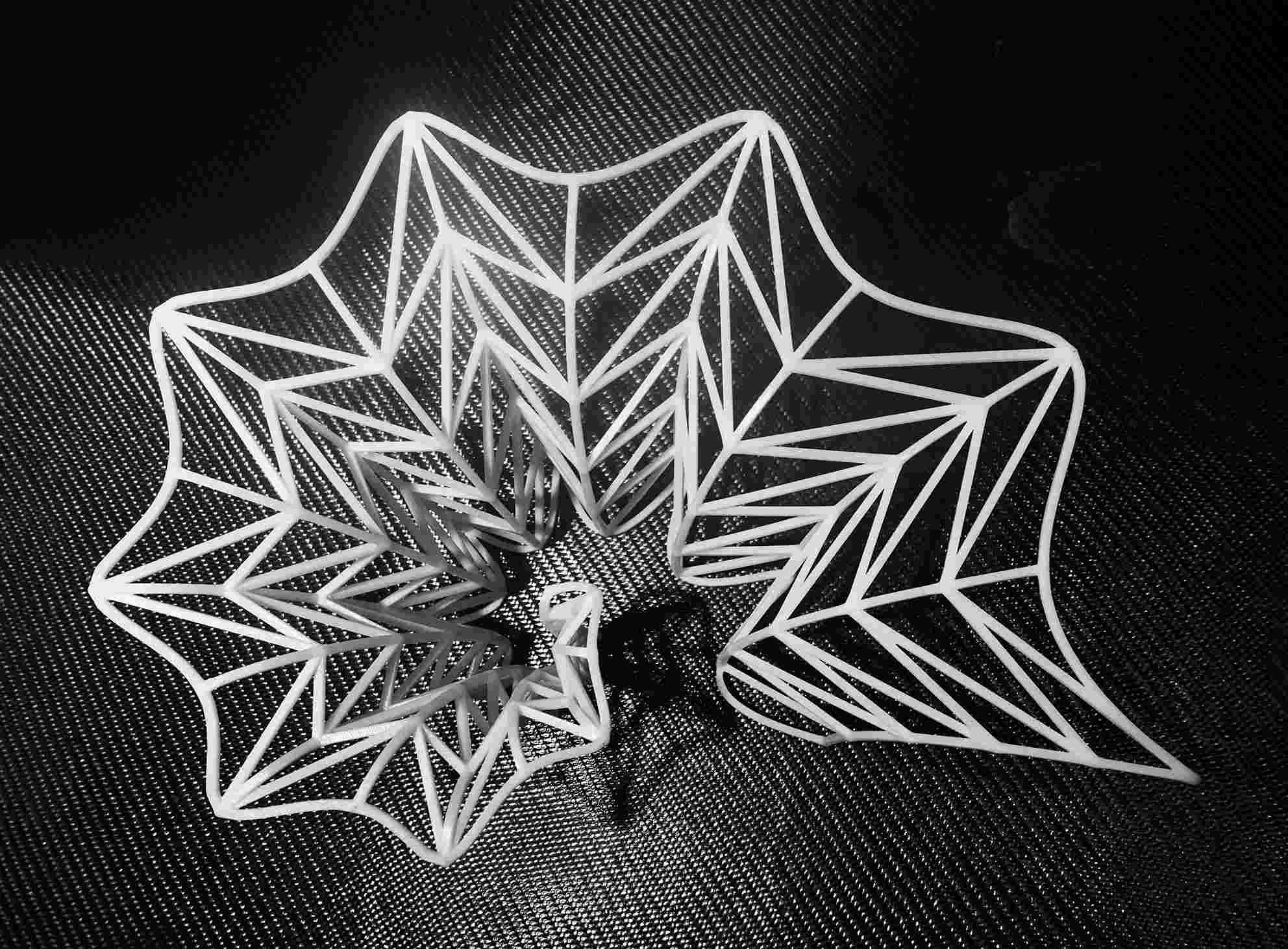
Force Follows Force 力学生形
Performance-based design and intelligent construction are the two main elements driving the future of architectural design. They are primarily reflected in the improvement of material performance, rational optimization of structures, and the intelligence of the construction process. However, the traditional construction model still operates in a relatively disconnected state, with design, structure, and construction processes remaining separate. This has led to issues such as mismatches between design form and structural performance, as well as discrepancies between optimized structures and construction details.
The aim of this research is to integrate materials, structure, and construction to realize the fusion of design and construction, while systematizing the flow of data to explore future digital architectural design approaches. The research focuses on the design and construction of a wooden pavilion, encompassing systematic design studies related to industrialized wood, structural performance optimization, and robotic intelligent construction.
性能导向设计与智能建造是引领未来建筑设计的两大核心要素,主要体现在材料性能的提升、结构优化的合理化以及建造过程的智能化。然而,传统的建造模式仍然处于设计、结构与施工相对独立的状态,导致了设计形态与结构性能的不匹配、优化结构与施工细节之间的错位等问题不断出现。
本研究的目的是通过材料、结构和施工的协同合作,实现设计与施工的融合以及数据流的系统化,探索未来数字化建筑设计的模式。本文的研究内容通过木质凉亭的设计与建造,结合工业化木材、结构性能优化和机器人智能建造等方面的系统性设计研究,探索建筑设计与建造的创新路径。
Design Framework 设计框架
The design and construction of the wooden pavilion are considered from three dimensions: design, optimization, and construction. These dimensions are interrelated and influence each other in a cyclical manner. The specific areas involved include form generation, parametric design, mechanical performance optimization, and robotic intelligent construction. 从设计、优化、建造三个维度综合考虑木构展厅的设计与建造。而这三个维度也会相互影响,循环作用。具体涉及领域如形态生成、参数化设计、力学性能优化、机器人智能建造等。
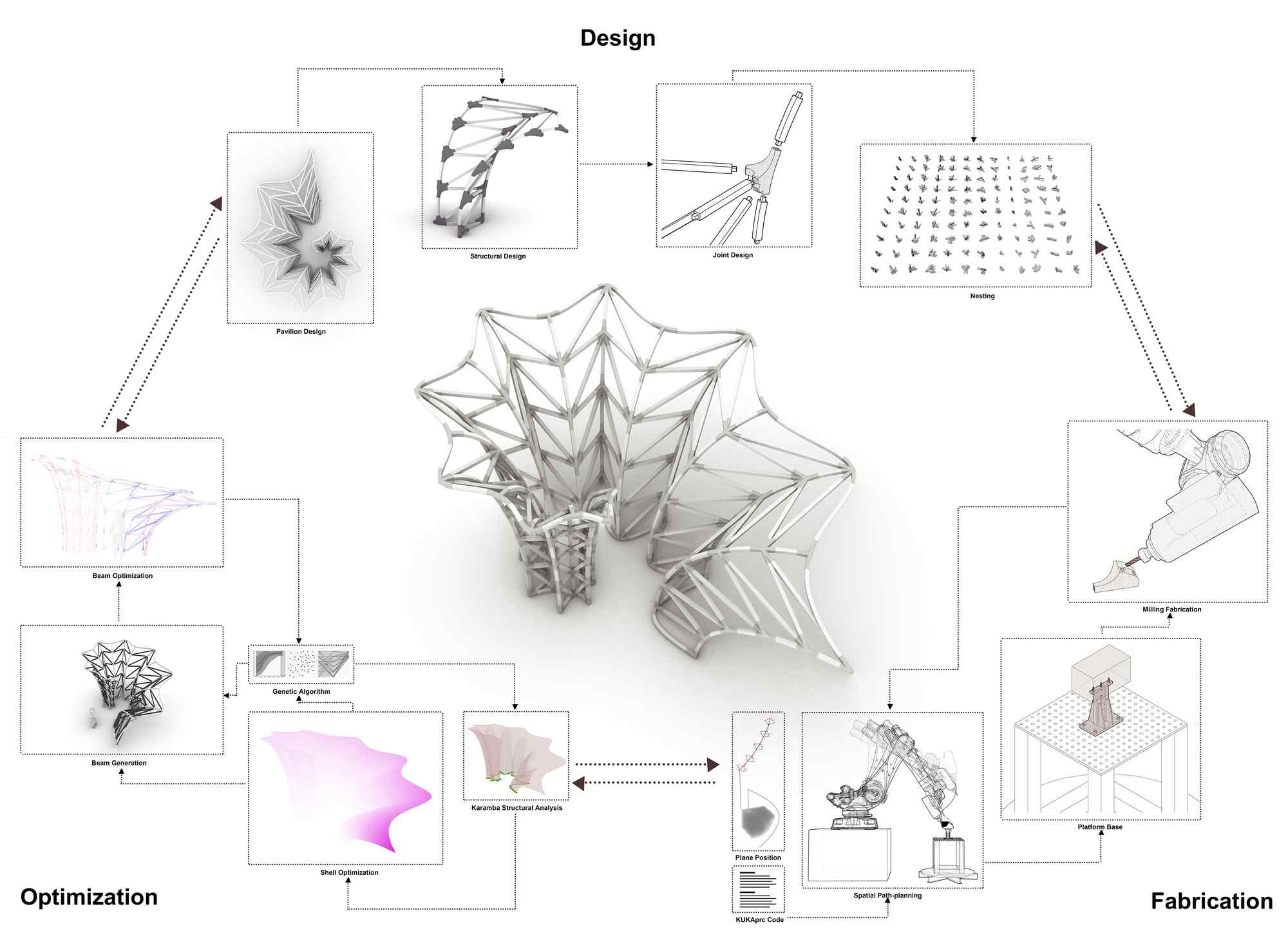
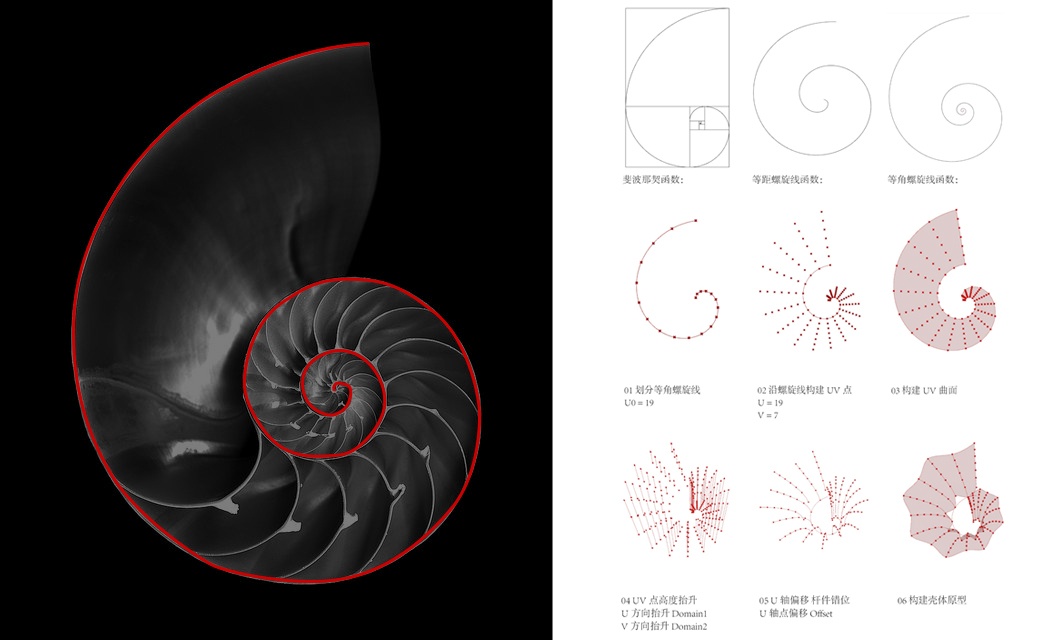
Design Form Generation 设计生形
The first step is the initial form generation of the overall design. Inspired by the skeletal structure of a nautilus shell, which naturally achieves stability, the design exteriorizes this structure into a shell form. An equiangular spiral is used to generate the planar prototype. Through parametric design, the planar UV grid is divided, and elevation and displacement are applied to create the initial shell structure. 第一步,是整体设计的初始生形。根据设计灵感来源于鹦鹉螺的骨骼结构外化为壳体,自身达成稳定的性能。因此以等角螺旋线生成平面原型。再通过参数化设计,划分平面UV网格,进行高度抬升与偏移,形成最初的壳体结构。
Structural Optimization 结构优化
The second step involves shell structure analysis and material selection. By setting optimization parameters for the variation of the shell form, such as the offset of internal and external convexities and the elevation height, the shell structure is analyzed using Karamba. Additionally, a genetic algorithm is applied for iterative analysis to minimize the structural strain energy and displacement. The overall optimized structure gradually evolves from a smooth surface into a stable form with varying cross-sections, characterized by concave and convex features. The third step involves the topological form generation, transitioning from a shell to a network of shell members. This includes the supporting curved beams, ring beams, and internal support rods, as well as the generation of complex joint connections at the ends. On this basis, Karamba is used to optimize the distribution of rod positions and layers to achieve minimal strain energy. Additionally, an optimization algorithm for the cross-sectional selection of rods in Karamba is applied, resulting in the most efficient structural rod cross-sections. 第二步,进行壳体结构分析与选型。通过设定壳体形式变化的优化参数,比如内外凹凸的偏移量,抬升高度等,利用Karamba进行壳体结构的分析,同时利用遗传算法进行迭代分析,以缩小结构的应变能以及偏移量。整体的优化结构,可以看出是壳体逐步从光滑的曲面优化成带有凹凸的类似变截面的稳定结构。 第三步,进行从壳体到网壳杆件的拓扑生形。分为支撑的曲梁与圈梁以及内部的支撑杆件。同时进行端头连接的复杂节点的生成。在此基础上,利用karamba进行杆件分布位置与层数的优化,达到最小应变能。同时,也进行了karamba的截面选杆算法的优化,得到结构最优的杆件截面。
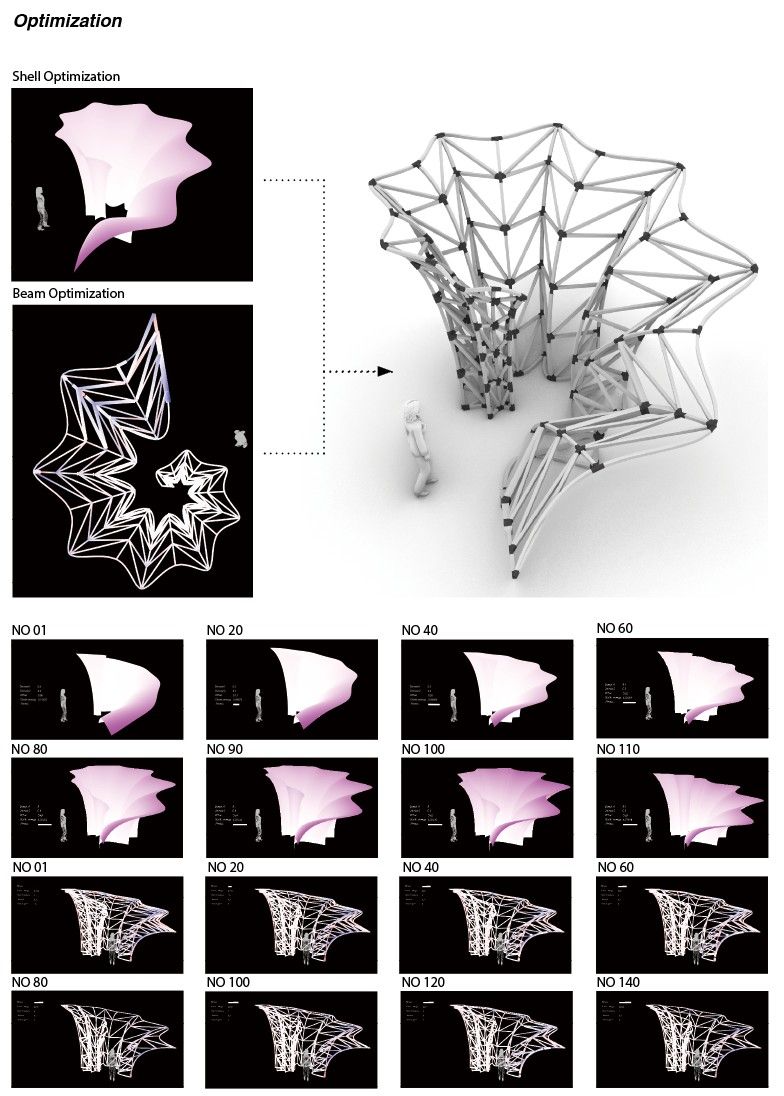
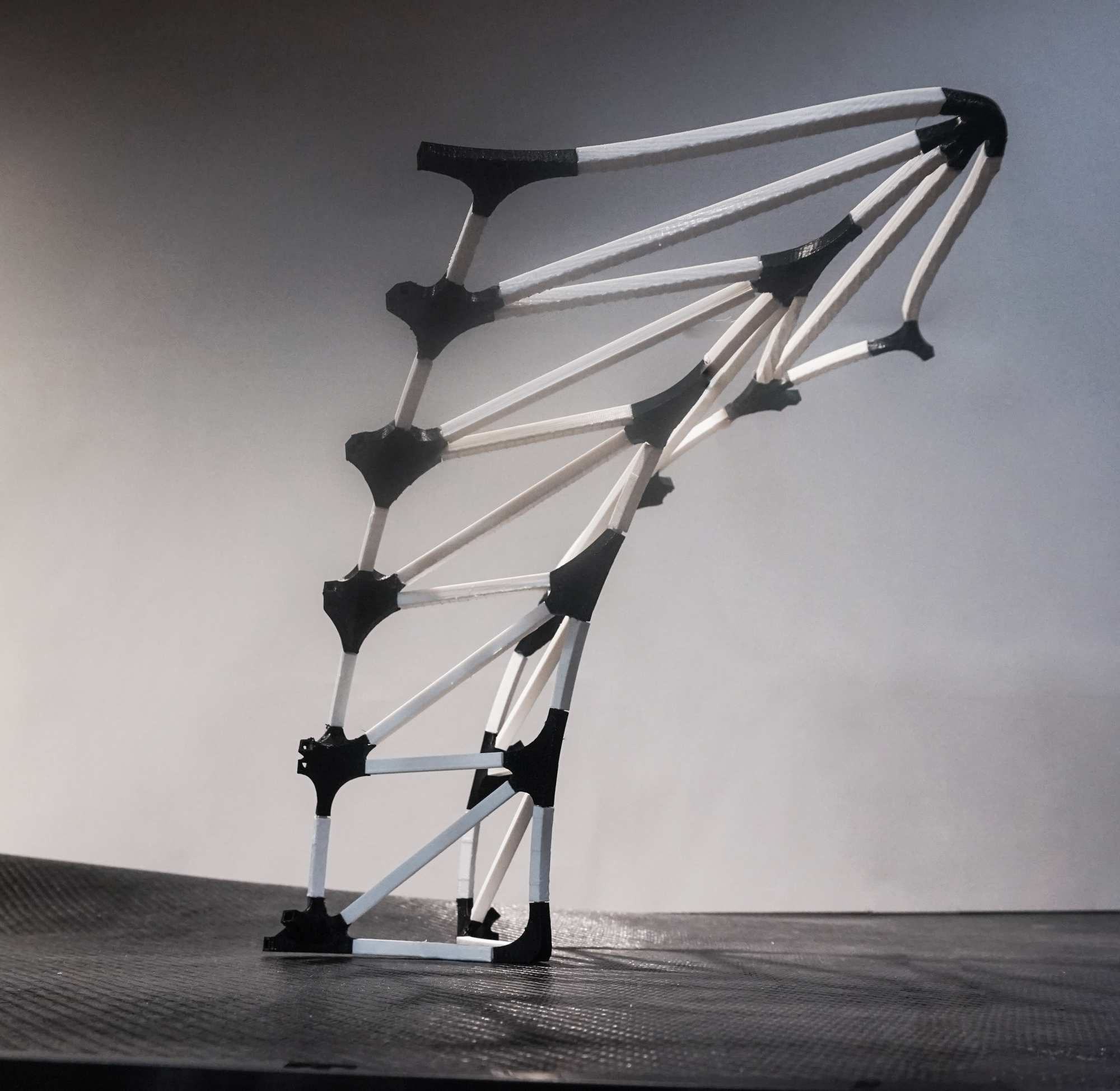
Joint Design 节点深化
The fourth step involves design refinement and digital fabrication. I categorize the construction components into three main types: wooden joints for milling, straight wooden rods, and curved wooden rods, each corresponding to different processing methods and techniques. The 120 joints will be fabricated using a six-axis robotic arm with a milling cutter. Curved beams will be flattened into two dimensions and, together with the straight rods, will undergo CNC machining. 第四步,是在设计的基础上,进行设计深化与数字建造。我将建造的构件分为三大类,包括木节点铣削、直木杆件以及曲木杆件,以对应不同的加工方式与工艺。120个节点建造将采用六轴机械臂配置铣刀铣削。曲梁做二维平面化处理与直杆一起采用CNC加工。
Robitic Fabrication 机械臂铣削加工
The wooden joints were fabricated using a 1:1 scale milling process. First, a steel support frame for the wooden joint processing platform was created, considering both the weight-bearing capacity of the wooden blocks and the stability during milling. The platform design also accounted for potential collision interference during the robotic arm’s path planning. Then, through robotic arm simulation and spatial path planning, the rough milling and fine milling paths were determined. The processing was completed at RoboticPlus technology company. 木构节点进行了1:1真实铣削加工。首先制作了木节点加工的基座平台钢支架,平台考虑了木块的承重与铣削时的稳定性,同时也考虑了机械臂路径规划过程中的碰撞干扰。然后通过机械臂仿真模拟与空间路径规划,确定粗铣与精铣的加工路径,在大界机械臂科技公司完成加工。
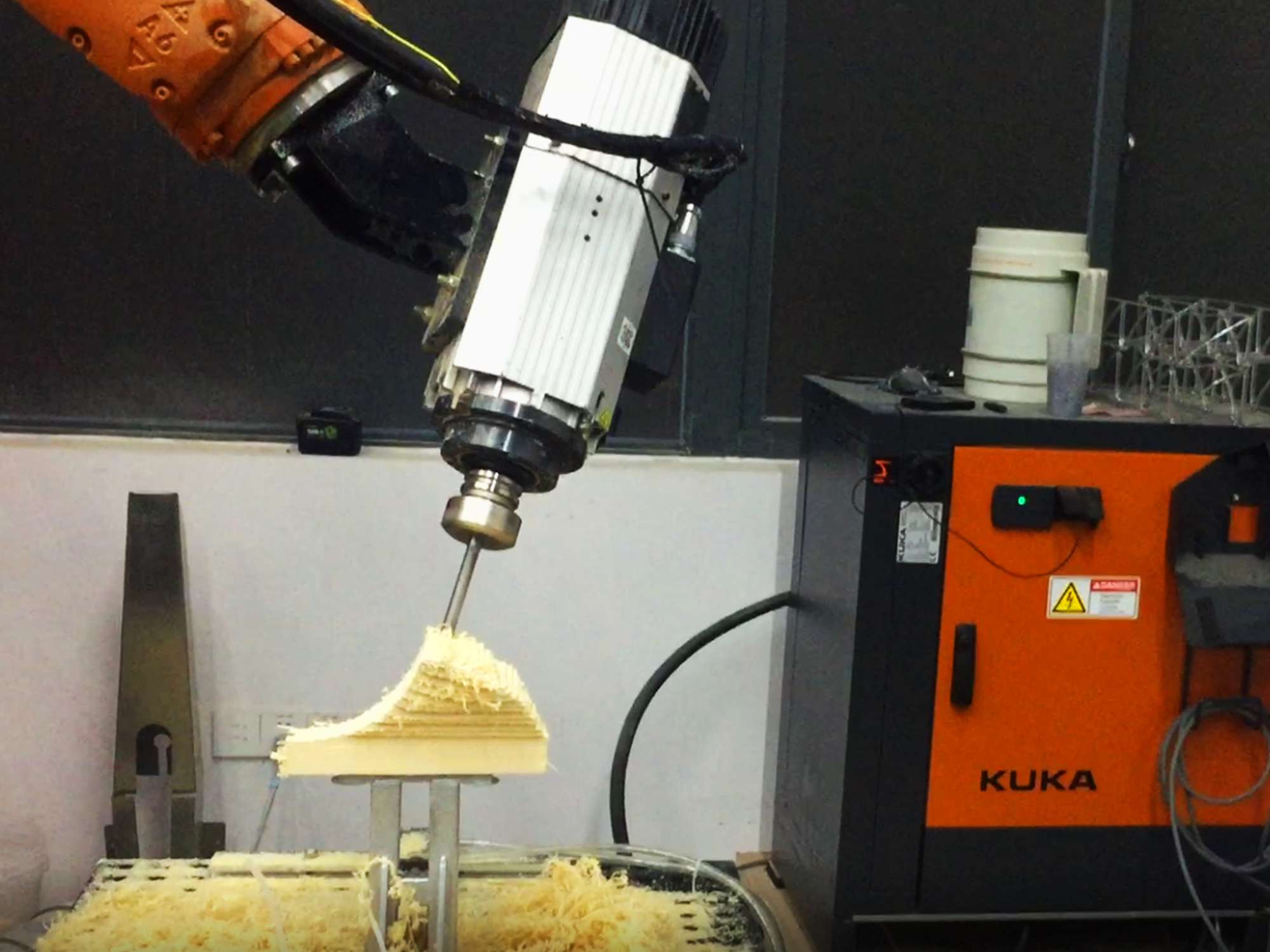
Drawing 图纸
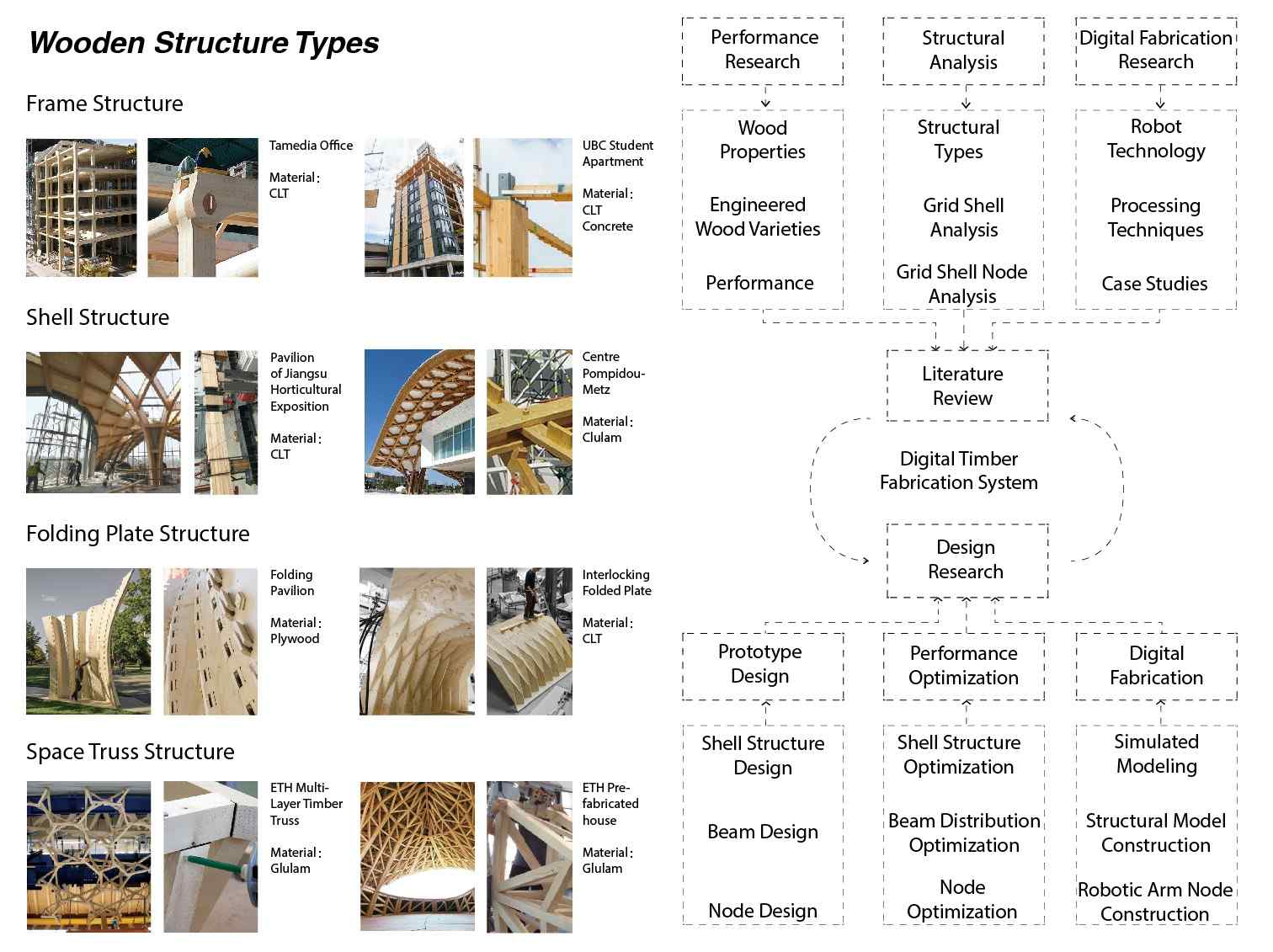
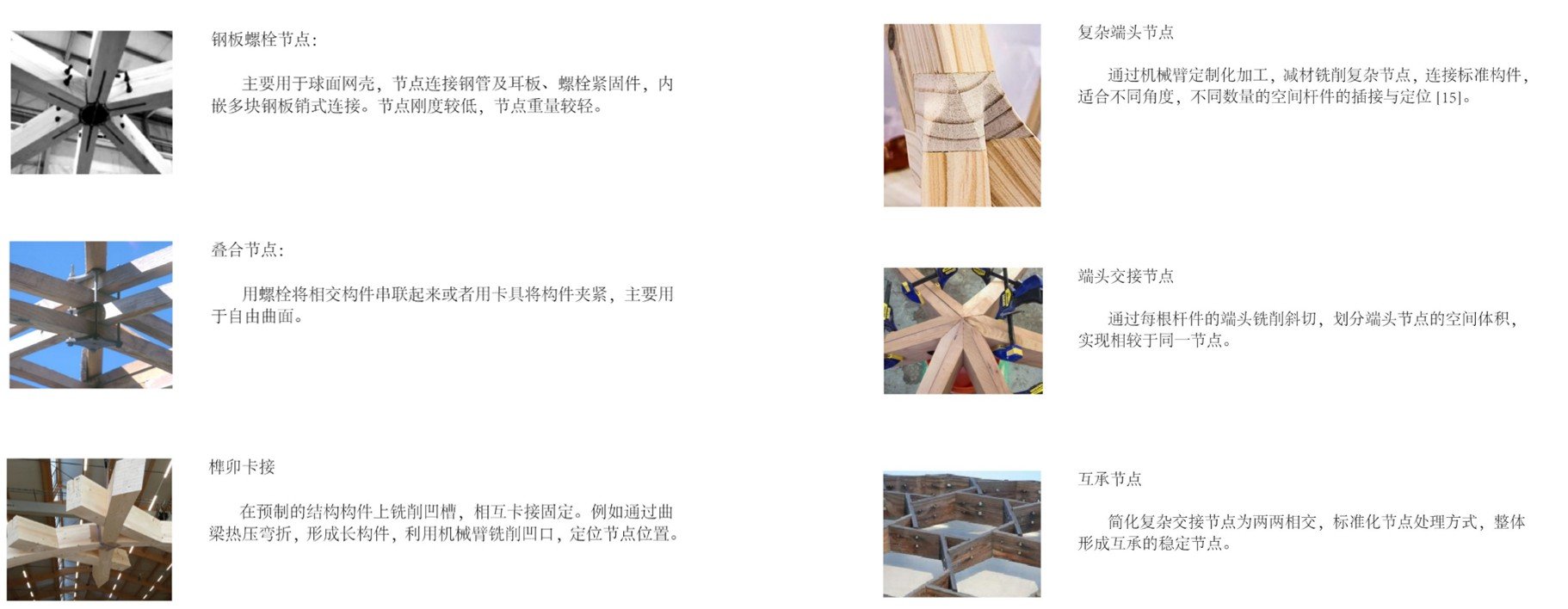
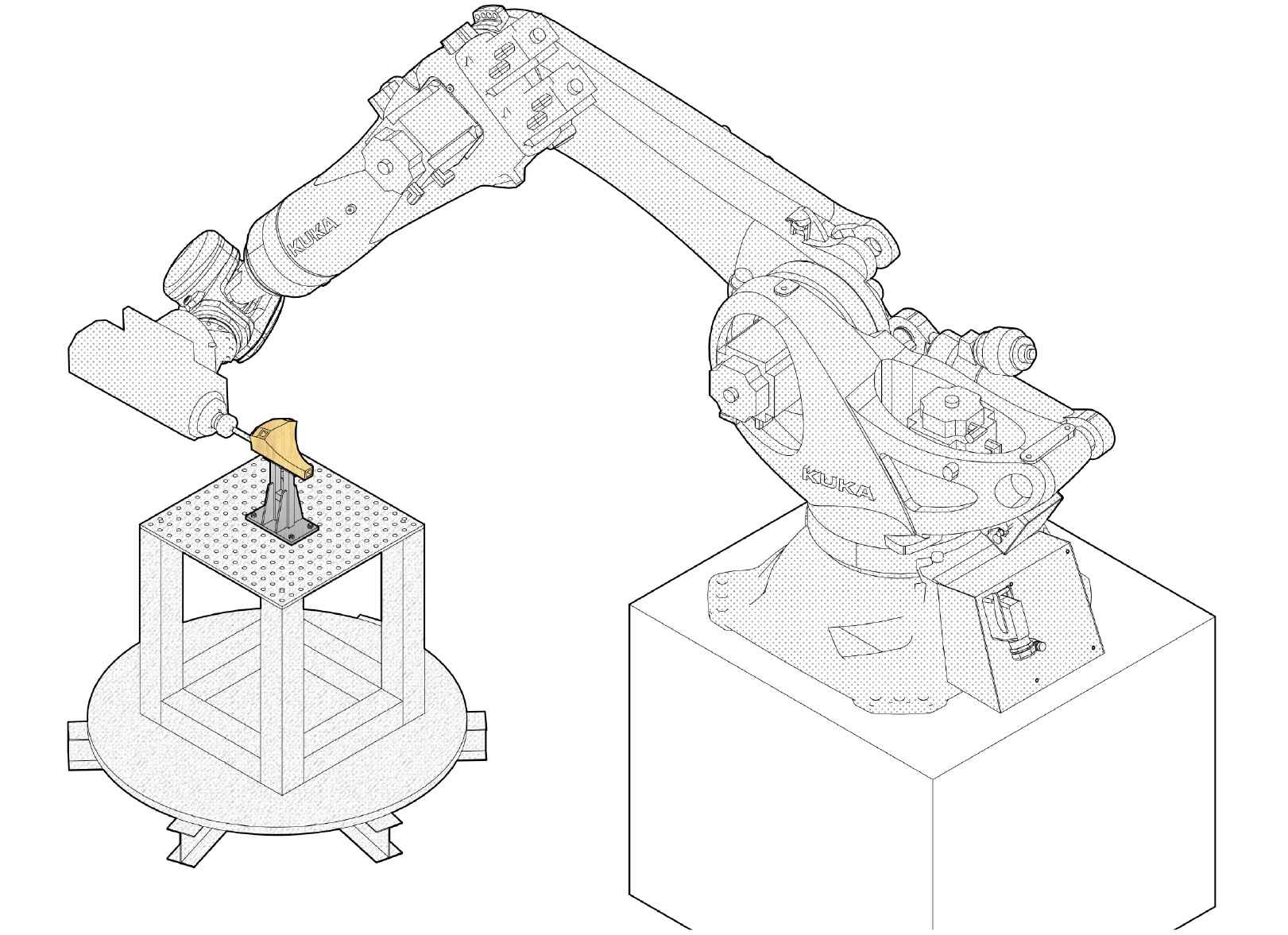
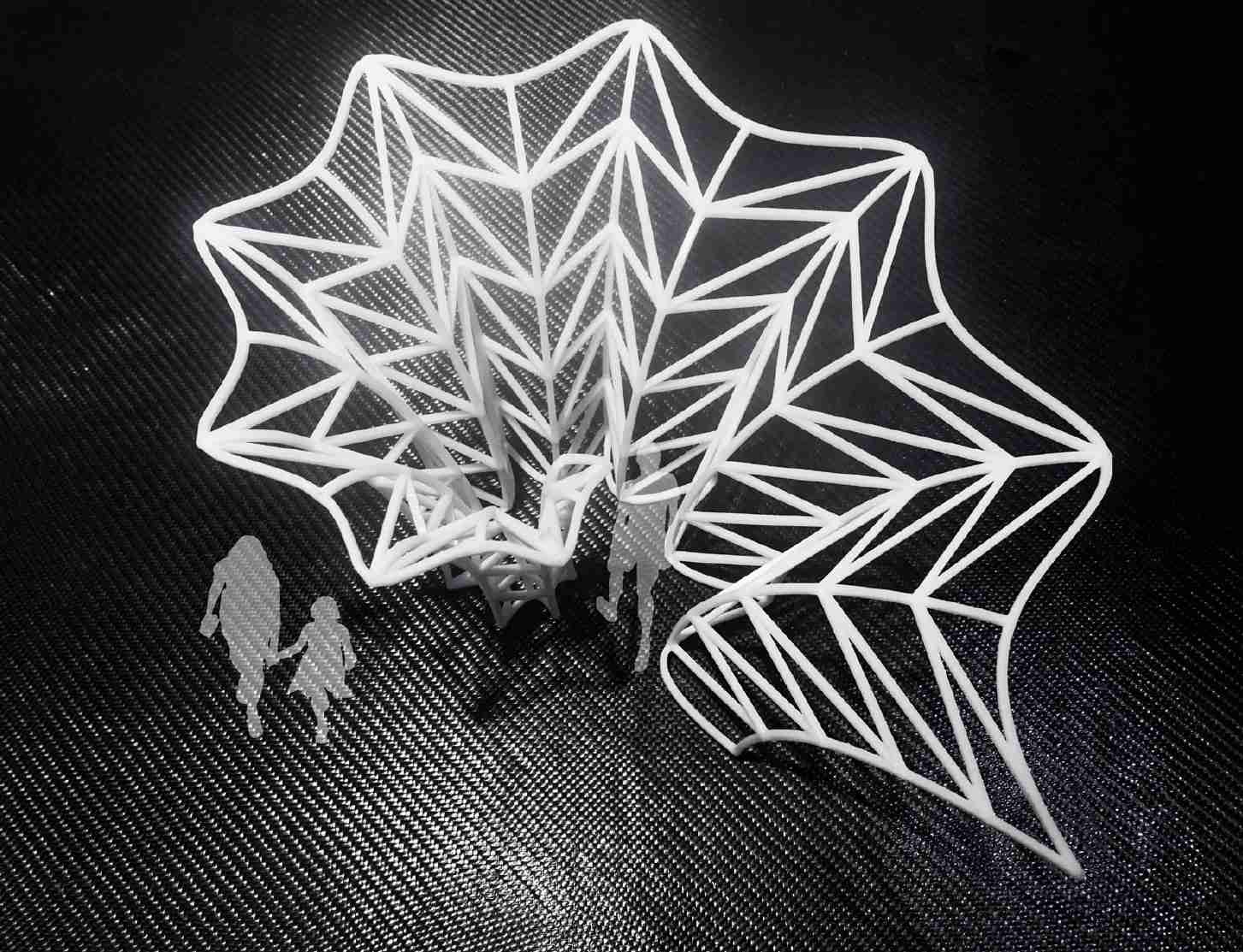